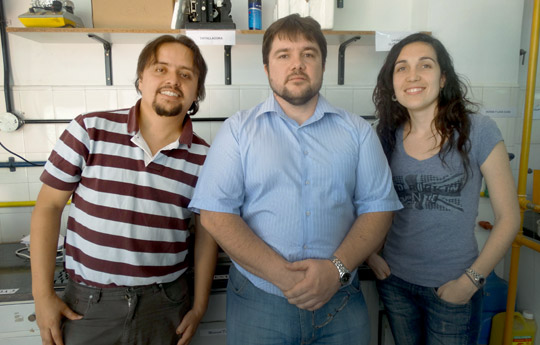
Londoño, Bilovol y Menchaca Nal. Foto: CONICET.
Científicos del CONICET desarrollaron un material nanoestructurado que tiene propiedades físico-químicas únicas y que, a futuro, permitirá innovar en materia de electrónica, salud y tecnología ambiental.
A simple vista parece una lámina negra y liviana, no muy diferente al papel carbónico.
Pero en realidad es un papel magnético desarrollado por científicos del Consejo, quienes sobre una base de fibras de nanocelulosa “adhirieron” nanopartículas de ferrita de cobalto – un material magnético – y generaron una lámina con esas mismas propiedades.
“La ferrita es un material muy usado por su magnetismo pero, cuando se sintetiza a escala nano, sus características físicas y químicas cambian mucho”, explica Vitaliy Bilovol, investigador adjunto del CONICET y coordinador del grupo de trabajo.
Cuando se reduce el tamaño de las partículas al orden de la milmillonésima parte de metro, sus propiedades cambian con respecto a la ferrita en estado masivo y, por ejemplo, por debajo de una temperatura específica su comportamiento magnético es diferente.
Esta propiedad podría, por ejemplo, usarse para fabricar sensores que mantengan la temperatura por debajo de cierto nivel y que cuando los valores superen determinado límite, se active un mecanismo que enfríe nuevamente el ambiente, una aplicación con potencial impacto en la industria alimentaria.
Además, algunos dispositivos como discos rígidos, parlantes y auriculares usan materiales magnéticos, y por sus dimensiones y características esta lámina podría llevar a innovaciones en diferentes campos, tanto en términos de funcionalidades como de tamaño de los dispositivos.
Otra aplicación posible es en el campo de la salud, donde estos nanomateriales pueden usarse como carriers de drogas.
“Con ayuda de un imán estos materiales con propiedades magnéticas específicas podrían usarse para dirigir medicamentos hacia el sitio de acción”, agrega Sandra Menchaca Nal, becaria doctoral del CONICET.
Y, por sus dimensiones, pueden viajar por el interior de los vasos sanguíneos, un requisito importante para el transporte de drogas.
Pero, ¿cómo se alcanza este nivel de precisión en el magnetismo?
La clave está en el tamaño
A pesar de que las propiedades magnéticas de la ferrita de cobalto son bien conocidas, cuando sus partículas se reducen a un tamaño de algunos pocos nanómetros adquieren un comportamiento característico conocido como superparamagnetismo.
“Un material magnético por lo general, cuando es de gran tamaño, se divide en los llamados dominios magnéticos, que son regiones que actúan como pequeños imanes.
El momento magnético es la propiedad que caracteriza el magnetismo del material.
Si al acercar un imán, la suma de los momentos magnéticos del material da cero, no tiene respuesta magnética apreciable; pero si es diferente a cero posee propiedades magnéticas de interés científico y tecnológico”, explica César Londoño Calderón, becario doctoral del CONICET y otro de los miembros del equipo.
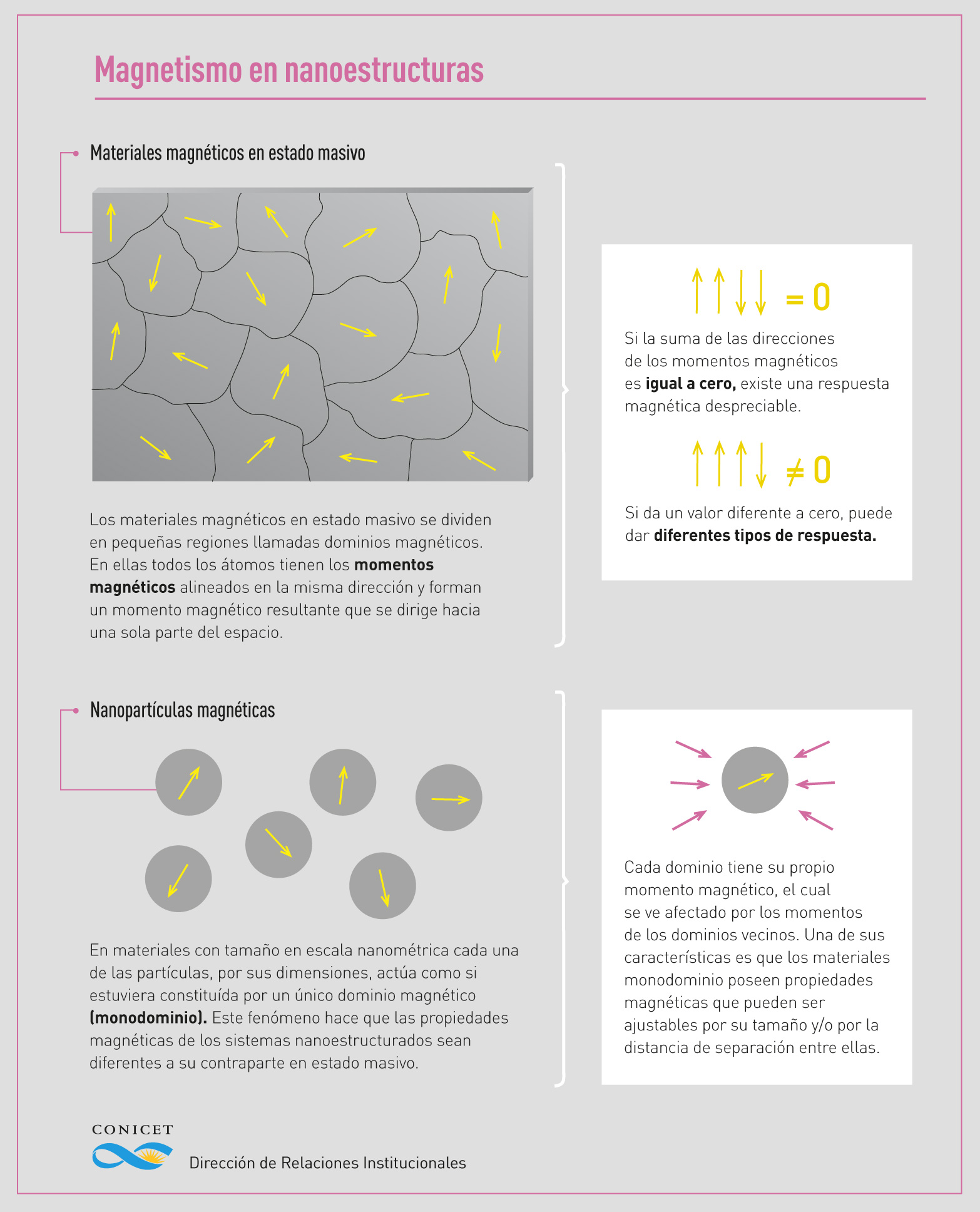
“A partir de diferentes técnicas se pueden sintetizar materiales de tamaño tan pequeño que tengan un solo dominio”, dice Bilovol.
Y eso fue justamente lo que hicieron con la ferrita de cobalto.
Pero, ¿para qué sirve un monodominio magnético? “Depende de la aplicación”, analiza Londoño Calderón, “por ejemplo, si se necesita fabricar el núcleo de un transformador se usa ferrita de cobalto con dominios magnéticos grandes.
Pero si necesitás un material que después de cierta temperatura se comporte de manera completamente diferente, se usan los materiales compuestos por monodominios”.
Nuevo instituto. Trabajo multidisciplinario
Menchaca Nal explica que la idea fue comenzar a trabajar con nanocelulosa porque otro grupo dentro del ITPN, liderado por la investigadora del CONICET Laura Foresti, desarrolló una técnica para producir ese compuesto.
Obtienen nanocelulosa de origen bacterial, que usan en diferentes investigaciones e incluso para el desarrollo de parches para heridas y piel quemada, entre otros proyectos.
“Como el instituto está recién creado, la idea era lograr una interacción entre los dos grupos de trabajo.
Nosotros aportamos las nanopartículas de ferrita de cobalto y ellos la nanocelulosa”, explica.
Así surgió la idea de hacer un papel magnético.
“Usamos el papel hecho a partir de nanocelulosa como plantilla para depositar la ferrita de cobalto en una forma determinada y después estudiamos sus propiedades físicas y químicas”, agrega Londoño Calderón.
La diferencia, explica Londoño Calderón, entre el material que obtenían al precipitar la ferrita de cobalto sin la plantilla, y luego en ella, tiene que ver con la homogeneidad de las nanopartículas, que es mayor en el segundo caso.
Así, el material obtenido combina las propiedades de la lámina de nanocelulosa y las magnéticas de la ferrita de cobalto.
A futuro el equipo del ITPN busca sintetizar estos nanomateriales en diferentes soportes que les confieran nuevas propiedades y permita a las partículas agruparse de diferentes formas con el objetivo de obtener aplicaciones innovadoras.
Por Ana Belluscio.
Sobre investigación:
Viltaliy Bilovol. Investigador adjunto. INTECIN.
César Londoño Calderón. Becario doctoral. ITPN.
Sandra Menchaca Nal. Becaria doctoral. ITPN.
conicet